Press and Bolster calibration
Introduction
Press and bolster plate calibration is a critical process in the stamping process that ensures optimal tool life, and quality of output part. It involves the careful adjustment and alignment of press machines and bolster plates to meet specific standards and requirements.
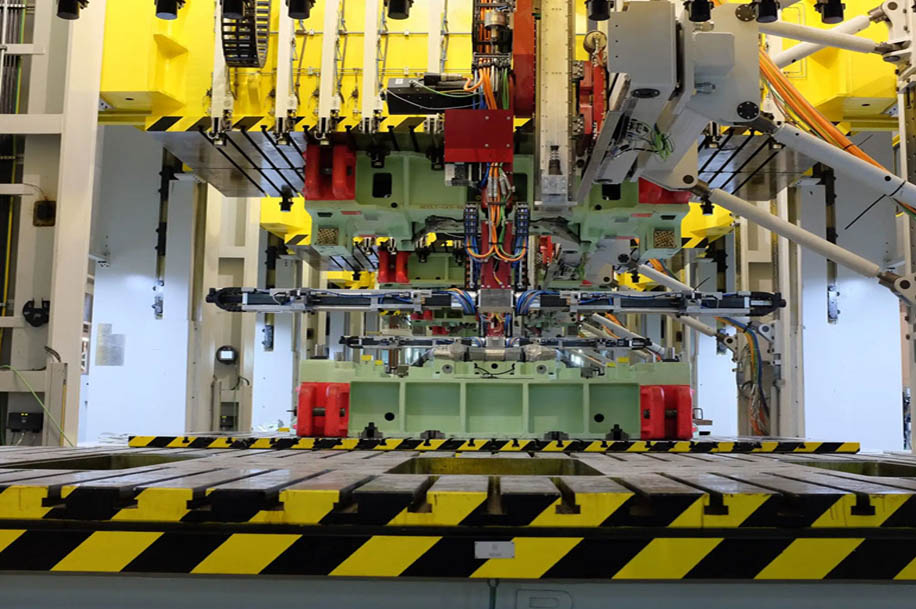
Services
Ensuring Precision and Accuracy
Press machines are widely used in manufacturing for a variety of applications, including forming, stamping, punching, and forging. The accuracy and precision of these processes heavily rely on properly calibrated press machines. By calibrating the press, manufacturers can fine-tune its settings to ensure precise control over factors such as force, speed, and stroke length. This calibration process eliminates variations and deviations that could compromise the integrity of the output part, leading to improved quality control.
Enhancing Efficiency and Productivity
Calibrating press machines and bolster plates optimizes their performance, leading to increased efficiency and productivity in manufacturing operations. A calibrated press machine operates at its peak performance, reducing downtime caused by equipment failures and minimizing the need for frequent maintenance. With precise control over variables such as force and speed, manufacturers can achieve faster cycle times and higher production rates, resulting in improved overall efficiency.
Quality Assurance and Compliance
In the stamping business, stampers must adhere to specific standards and regulations to ensure the quality and reliability of their products. By calibrating press machines and bolster plates, stampers can verify that their equipment meets the necessary specifications. This not only helps ensure the consistency and accuracy of the manufactured products but also demonstrates compliance with tooling HLTO requirements.
Cost Savings
Effective calibration practices can lead to cost savings in the long run. By regularly calibrating press machines and bolster plates, manufacturers can detect and address minor issues before they escalate into major problems. This proactive approach helps minimize equipment breakdowns, reduce the need for expensive repairs, and extend the lifespan of the machinery and tooling. Moreover, accurate calibration enables manufacturers to optimize material usage and minimize waste, resulting in significant cost reductions and improved profitability.
Press and bolster plate calibration are vital components of the manufacturing process. From ensuring precision and accuracy to enhancing safety, efficiency, and compliance, calibration plays a pivotal role in maintaining high-quality standards and achieving operational excellence. By investing in regular calibration procedures, manufacturers can improve their productivity, reduce costs, and deliver superior products to their customers.